5G e IIoT revolucionam a plataforma SCADA e impõem novos desafios à indústria brasileira
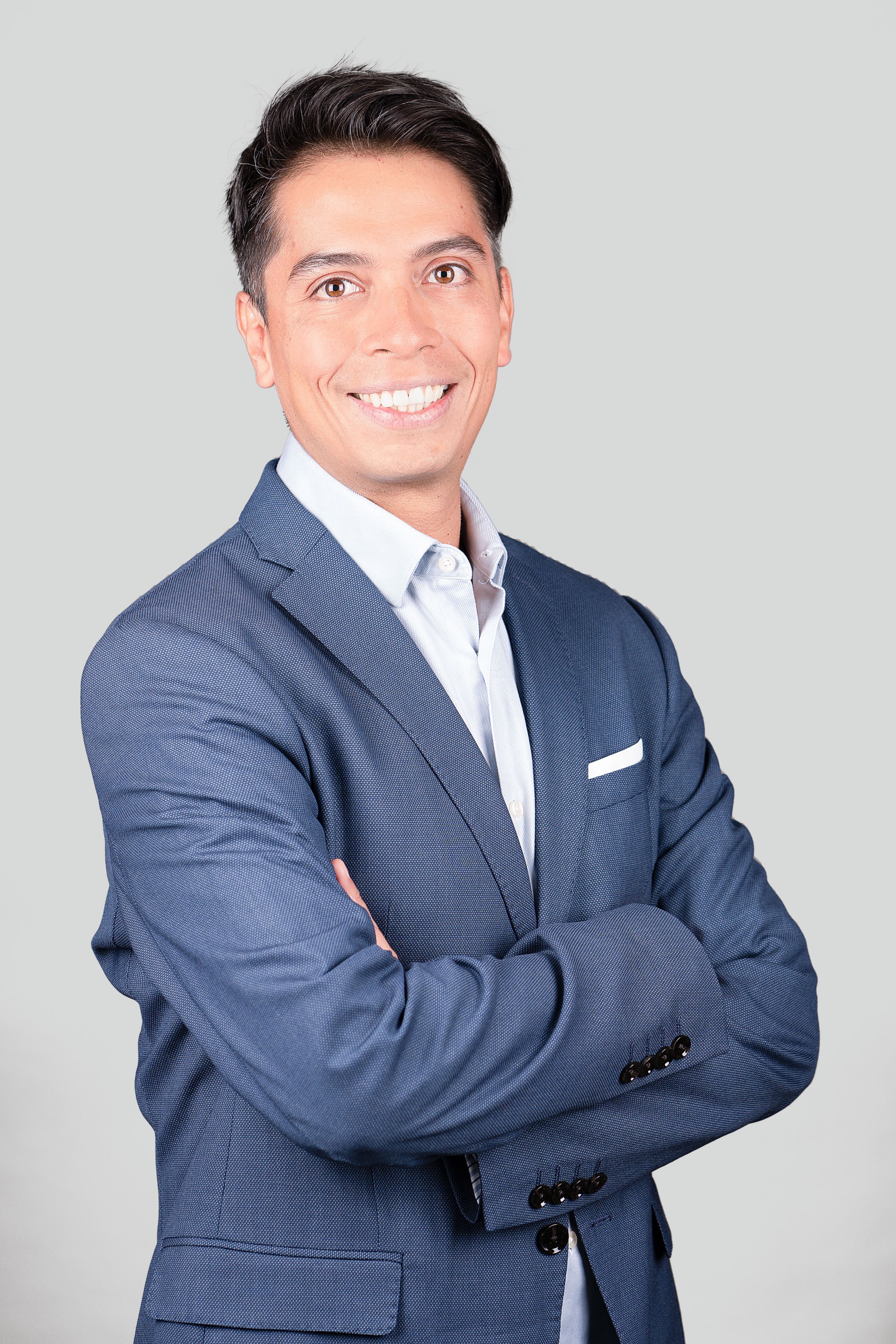
06.04.2023
Por David Montoya*
No Brasil e no mundo, o sistema Supervisory Control and Data Acquisition (SCADA) é o padrão de fato de indústrias de data centers, óleo e gás, alimento e bebidas, papel e celulose, farmacêutica, tratamento de água e até mesmo edifícios inteligentes. Esta plataforma permite à organização controlar processos industriais, coletando e processando dados em tempo real. Para isso, o SCADA interage com dispositivos críticos como motores, geradores, bombas, esteiras, sensores e válvulas. Arquivos de logs retratam tudo o que se passa no chão de fábrica. A força do ambiente SCADA em todas as verticais industriais é tal que, de acordo com estudo da Precedence Research, o valor global deste mercado, que era de USD 35,38 bilhões em 2021, deve chegar a mais de USD 61,22 bilhões até 2030.
A crescente integração de soluções da Indústria 4.0 à plataforma SCADA e o uso de inovações como 5G, Internet Industrial das Coisas (IIoT) e inteligência artificial (IA) estão por trás dessa estimativa. Outra forte tendência é o uso de análises de big data sobre o mar de dados SCADA, frequentemente mal explorado pelas organizações.
Fica claro que o SCADA está em processo acelerado de reinvenção – o contexto em que as primeiras implementações SCADA aconteceram no Brasil, décadas atrás, é totalmente diferente do atual. Uma das novas premissas é a convergência entre áreas industriais e a área de TI. É essa conexão que permite, por exemplo, a aceleração da fabricação on-demand de produtos customizados e em menor volume. Para isso, as áreas de OT e IT da indústria têm de operar de forma integrada e em tempo real.
Pesquisa realizada pela Deloitte do Reino Unido em 2019 com 500 executivos do C-Level mostra que 14% desse grupo estava ativamente investindo na integração OT/IT. Trata-se de um processo difícil, com armadilhas no trajeto. Uma delas é a crescente vulnerabilidade dos ambientes industriais a ataques cibernéticos. O mesmo estudo da Deloitte informa que, desse total, 90% dos entrevistados afirmaram ter sofrido ataques digitais nos últimos dois anos - vazamento de dados confidenciais e a interrupção dos processos industriais foram alguns dos problemas enfrentados por essas empresas.
No caso de indústrias operando com apoio de sistemas SCADA, uma parada causada ou por ataques digitais ou por falhas na infraestrutura de networking pode provocar imensas perdas.
Prejuízo de milhões de Euros na Norsk Hydro, na Noruega
Um dos episódios mais emblemáticos de ataques contra ambientes industriais SCADA aconteceu em 2019 com a gigante norueguesa de fabricação de aço Norsk Hydro. O exploit de ransomware utilizado bloqueava o acesso a esses sistemas críticos. O bloqueio criminoso durou vários dias, quase imobilizou a linha de produção - foi necessário recorrer a notas fiscais e planilhas em papel para dar continuidade aos processos da Norsk Hydro - e gerou prejuízos de 45 milhões de Euros (cerca de R$ 301 milhões).
Esse tipo de incidente atesta a nova realidade da plataforma SCADA, que por anos operou isolada das infraestruturas de TI e fora do alcance dos cibercriminosos. Hoje, as fábricas estão conectadas a redes de computadores – uma das conexões mais críticas é entre o ambiente SCADA e sistemas de ERP como o SAP – e também ao mundo externo. A proteção do chão de fábrica passa pelo uso de soluções de segurança e, também, por inovações em monitoração que aumentam as garantias de continuidade nas indústrias de processos.
Eu acompanhei um projeto OT/TI em um cliente no México que já era usuário de soluções de segurança no chão de fábrica. Durante o andamento do trabalho, identificamos um problema com um endereço IP específico. O fato gerou surpresa dos gestores, já que havia firewalls protegendo a rede industrial. Ao verificar o que poderia estar acontecendo, foi diagnosticado que o firewall, por algum motivo, estava desabilitado. A rede que suportava o sistema SCADA estava, portanto, vulnerável a ataques.
Por sua natureza, SCADA oferece uma visão limitada sobre a rede
Engenheiros de processos não conseguem obter dados de dispositivos como sensores IIoT ou outros tipos de computadores usando sua rede atual de chão de fábrica. Para entender este desafio, é necessário detalhar um pouco a arquitetura SCADA. O SCADA é formado por componentes de hardware e software. O hardware é responsável por coletar e alimentar dados para um computador com software SCADA instalado. Durante o processo industrial, uma aplicação SCADA emitirá um aviso ou soará um alarme quando as condições se tornarem perigosas ou fora de parâmetros.
Para isso, o SCADA funciona da seguinte maneira:
· O sistema começa comunicando-se diretamente com os controladores em campo em tempo real, geralmente por meio de CLPs (Controladores Lógicos Programáveis). Isso é feito com o suporte de uma rede física, com cabos de cobre, implementada no chão de fábrica.
· Em seguida, o sistema SCADA reúne todos os dados obtidos pelos conectores em campo e os transfere para o próprio SCADA – normalmente um servidor também instalado no ambiente industrial.
·Os dados são mostrados graficamente aos operadores em Human Machine Interfaces (HMI), usadas pelos profissionais para executar os processos industriais.
•Com a chegada ao Brasil da rede 5G, esse contexto, inalterado há décadas, está passando por uma profunda transformação. A rede wireless baseada em dispositivos IIoT irá cada vez mais se mesclar à tradicional rede SCADA. Outra mudança expressiva é a estreita interação entre o SCADA e aplicações que, agora, irão muito além do ERP. A riqueza de dados gerada pelo SCADA passa a ser vista como um patrimônio de toda a empresa, que deve ser utilizada em análises e estratégias financeiras, de marketing etc.
Indústria 4.0
Tudo isso faz parte da Indústria 4.0 e impõe grandes desafios aos gestores. Há um aumento da complexidade, além da necessidade de se integrar perfeitamente uma gama mais ampla de sistemas e dados. Isso acontece em meio à ameaça de ataques cibernéticos.
Neste contexto, torna-se essencial conectar de forma segura e controlada novíssimas tecnologias à rede e ao hardware legados do SCADA. Esse é o papel de soluções que oferecem conectividade OPC UA e drivers nativos que suportem equipamentos mais antigos. O protocolo de comunicação OPC UA é amplamente utilizado para permitir que diferentes sistemas se conectem entre si sem a necessidade de ocultar dados, usar gateways ou traduzir os dados de uma linguagem para outra.
O Brasil conta com plataformas de monitoração que, por suportar nativamente o protocolo OPC UA, mergulham nos meandros do chão de fábrica. Isso acontece em paralelo à conexão entre os universos OT e IT, oferecendo uma visualização preditiva que equaciona as crescentes demandas de integração entre a área de produção e os times de marketing, logística etc. O resultado dessa abordagem é uma nova clareza sobre um universo complexo e em constante expansão. Deixa de ser necessário reconfigurar o SCADA, algo extremamente complexo e caro. A solução de monitoramento acopla-se às configurações do SCADA, projetando no próprio ambiente SCADA – na Human Machine Interface – a visualização sobre toda a rede de chão de fábrica. Isso vale para CLPs, sensores IIoT, firewalls, roteadores e computadores de várias arquiteturas.
Quem adotar esta estratégia acelerará a transformação digital da indústria usuária de SCADA. A meta é facilitar a conquista de novas marcas de competitividade global para um setor crítico da economia brasileira.
*Gerente Global de Desenvolvimento de Negócios de IoT da Paessler